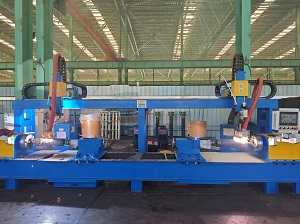
一、连铸辊堆焊技术概述
连铸辊是钢铁连铸生产线的核心部件之一,长期在高温、高压、强磨损及腐蚀性环境下运行,容易出现表面裂纹、磨损、剥落等损伤。传统解决方案是直接更换新辊,但这种方式成本高昂,采购周期长,且频繁更换会影响生产连续性。
连铸辊堆焊技术通过在磨损辊体表面熔覆高性能耐磨合金材料,可有效恢复辊子尺寸并增强其抗磨损、耐高温和抗腐蚀性能。相比整体更换,堆焊修复可显著延长辊子使用寿命,降低维护成本,已成为现代钢铁企业优化设备管理、提升生产效率的重要手段。
二、堆焊设备的高效性体现
1. 快速修复能力
连铸辊堆焊设备采用高度自动化操作流程,从表面预处理(如清理、打磨)到堆焊熔覆、后处理(如热处理、机加工)均可高效完成。相比传统人工焊接或更换新辊,自动化堆焊大幅缩短了修复周期,使连铸生产线停机时间最小化,确保生产连续性。
2. 材料利用率高
堆焊技术仅针对辊子的磨损部位进行材料增补,而非整体更换,因此可大幅减少金属材料的消耗。同时,堆焊使用的合金粉末或焊丝可根据磨损情况精准匹配,避免资源浪费,符合绿色制造理念。
3. 工艺稳定性强
现代连铸辊堆焊设备配备精密控制系统,可实现焊接参数(如电流、电压、送丝速度、预热温度等)的精准调节,确保堆焊层均匀、致密,减少气孔、夹渣等缺陷,提高修复质量的一次合格率,降低返修率。
4. 适应多种工况
不同连铸辊(如结晶器辊、扇形段辊、拉矫辊等)的工况差异较大,磨损形式也各不相同。先进的堆焊设备可针对不同辊型、磨损程度及使用环境,灵活调整工艺参数,如采用不同合金材料(如钴基、镍基或铁基合金)进行定制化修复,确保修复后的辊子满足特定工况需求。
三、效率提升的配套技术
1. 自动化控制系统
采用PLC或CNC控制技术,实现焊接路径、速度和参数的自动调节,减少人工干预,提高作业精度和一致性。
2. 在线监测技术
通过红外测温、超声波检测或机器视觉技术,实时监控堆焊过程中的熔池状态、温度分布及焊接质量,及时发现并修正缺陷,避免后续返工。
3. 智能预热系统
堆焊前对辊体进行均匀预热,可减少焊接应力,防止裂纹产生;智能温控系统可动态调整加热参数,确保堆焊层与基体的结合强度。
4. 后处理一体化
部分高端堆焊设备集成了热处理、机加工(如车削、磨削)等功能,修复后可直接进行精加工,减少工序切换时间,提高整体效率。
四、行业应用价值
连铸辊堆焊技术的高效性不仅体现在单次修复作业中,更能为钢铁企业带来长期综合效益:
降低备件采购成本:减少新辊采购频率,延长辊子使用寿命,降低备件库存压力。
减少设备停机损失:快速修复可缩短产线停机时间,提高设备利用率。
优化生产维护计划:通过定期堆焊修复,企业可制定更科学的设备维护策略,避免突发性故障。
提升连铸生产线综合效率:稳定的辊子性能可减少铸坯表面缺陷,提高连铸生产质量和连续性。
五、未来发展趋势
随着智能制造和材料科学的进步,连铸辊堆焊技术正朝着更高效率、更高质量、更低成本的方向发展:
智能化升级:AI算法优化焊接参数,机器人自动化堆焊,减少人工依赖。
绿色堆焊工艺:减少能耗和废气排放,符合可持续发展要求。
六、结语
连铸辊堆焊技术凭借其高效修复能力、材料节约优势和工艺稳定性,已成为钢铁行业设备维护的重要解决方案。未来,随着技术的不断创新,堆焊修复将在提高生产效率、降低运营成本方面发挥更大作用,助力钢铁企业实现高质量发展。
以上内容由堆焊设备厂家天津雷公焊接材料有限公司编辑 咨询电话:18202593233
|